Case Study: Solving Motor Inrush Current and Energy Savings with VFDs
Tensions resolved between utility company and local community by replacing soft start with VFD to correct voltage sags due to medium voltage compressor starts
A large land fill energy producer in Chicago faced a big problem that caused the local community significant frustration and cost the producer over $200,000 a week in downtime. This problem all started from a 2250HP 4160V compressor motor used to compress reclaimed biogas from the landfill.
Despite the use of a Reduced Voltage Soft Starter (RVSS), the Compressor motor was drawing too much current from a weak distribution system every time it started, causing the voltage to drop in neighboring residential areas. The voltage drops resulting from the motor start caused many problems in the neighborhood, shutting off Televisions, resetting computers, and causing dimming and flickering lights in homes. After numerus calls of complaints from the community, the utility company chose to take action.
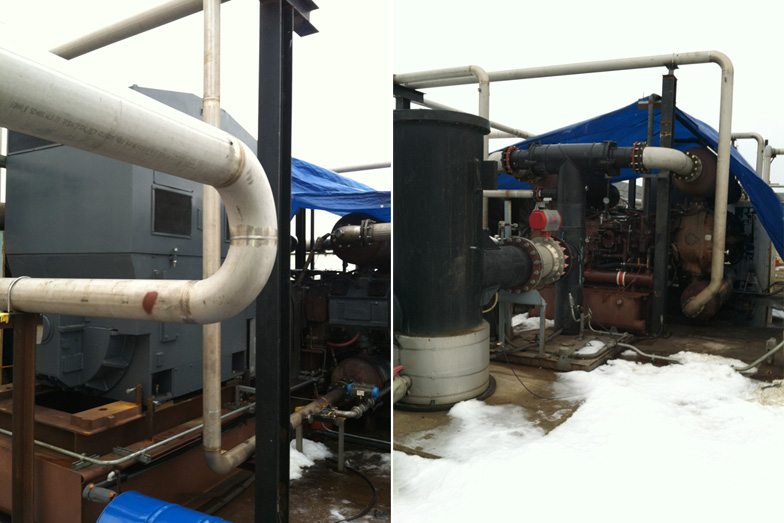
Case Study: Solving High Current Motor Starts and Energy Savings with Variable Frequency Drives
Market: Power Production + Oil/Gas
Equipment Type: 2250HP Compressor Motor, 2500HP 4160V Medium Voltage VFD
Project Scope: Eliminating the large startup current that caused voltage drop in neighborhood
Problem: 2250HP 4160V Compressor motor drawing in too much current and causing voltage drops to the surrounding community.
Solutions: A medium voltage VFD was installed to eliminate the high current associated with starting the compressor motor. Additional energy savings of $100,000 per year were also realized
Cease-and-desist:
Because of the consistent problems due to the motor’s starts, the utility company would no longer allow the 2250HP compressor to run. A Cease-and-desist letter was sent, and the landfill energy developer faced shut down costs of $30,000 a day. They needed a solution, and they need a solution fast.
The landfill energy producer needed to find a way to stop their compressor from drawing so much current on start-up so the local community wouldn’t experience the voltage drops and reached out to the team at VFDs.com for help. Since they already had a soft start but were still seeing a higher than acceptable inrush current, we began to investigate different options and engineering a solution with them.
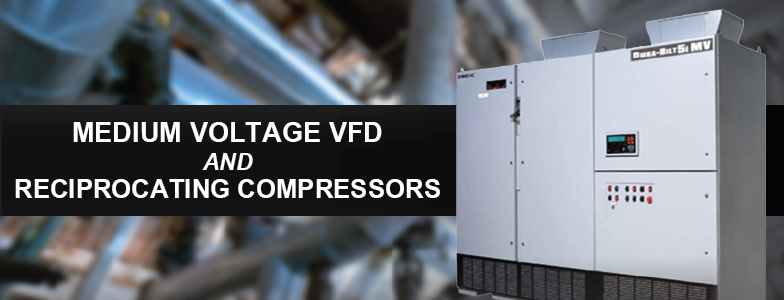
Solution:
Variable Frequency Drives have an advantage of being able to give the proper volts per hertz ratio to the electric motor throughout the speed range which help the ability to control torque and eliminate inrush during the starting process of the motor. VFDs not only have the ability to eliminate the high currents associated with starting a large motor, but they also have a very high displacement power factor, which further helps reduce the voltage drops.
With a solution identified, the difficulties of finding a manufacturer that could deliver and install a VFD with a quick turnaround time became a challenge. Since most Medium Voltage VFDs are used on applications that involve very specific requirements and configurations, it was unlikely that a manufacturer would have an option fitting their needs in stock and readily available.
Average lead times for manufacturing Medium Voltage VFDs can take anywhere from 16 to 20 weeks, which was time the landfill energy producer could not afford given the high production losses. In addition to the challenge of finding a manufacturer, the upcoming holiday season created additional concerns. Shortened manufacturing schedules, potential shipping delays, and whether an experienced engineer would be available for start-up and programming were all major concerns.
Result:
Fortunately, with VFDs.com, all of these concerns were addressed and solved. The customer placed their order on December 18, and the VFD shipped to the facility before Christmas. Considering the complexities and difficulties associated with providing a Medium Voltage Drive so quickly, the turnaround and delivery were significant.
An engineer from VFDs.com traveled to the facility over the holiday weekend between Christmas and New Year’s to oversee the start-up and programming. When that was completed, it was time for the true test. Did it fix the actual problem?
A call to the utility company was made and the landfill energy developer was given the green light to start their compressor again. The VFD did its job so well that the utility operator had to ask if the compressor had even been turned on yet since the voltage remained steady on their testing equipment. As a result, the customer was given permission to operate again bringing their downtime to an end. There have been no customer complaints concerning voltage drops caused by the compressor since the installation of the VFD at the facility.
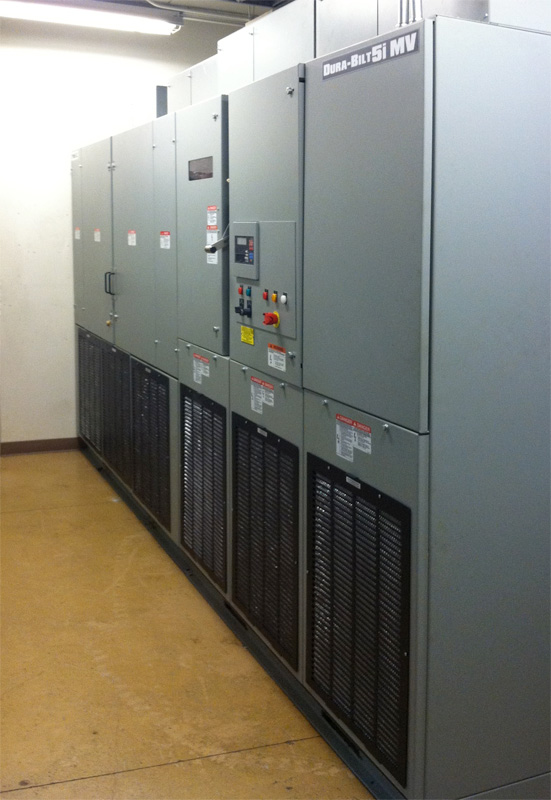
Additional Considerations and Benefits from the Variable Frequency Drive (VFD)
The VFD was the solution for the compressor’s high starting current and voltage drops, but it can also cause power quality problems on electrical grids. To ensure that the VFD implemented at the facility did not create yet another utility problem, a 24-pulse VFD was supplied. By using a 24-pulse system, negligible harmonic distortion is produced and any potential problems with harmonics and power quality are averted.
If no plan had been in place to control the high frequency noise from the VFD, it is possible that additional power quality problems could have been created, eventually leading to additional conflicts with the neighborhood and utility company.
Another benefit of implementing the VFD to the compressor was the significant energy savings generated as a result. During the commissioning and tuning of drive our VFDs.com engineer was able to recognize that the compressor was creating excess compression and using discharge valves. Though it was not part of the initial scope, we were able to reduce the speed of the motor which then required less energy to operate the compressor. This meant more energy was available for sale going back to the grid. The energy savings realized for this specific facility had produced verified savings more than $100,000 per year. This helped the customer quickly recoup the investment and help improve their operating costs.
VFDs.com and EMC
Based out of Salt Lake City, Utah, VFDs.com is a division of Energy Management Corporation (EMC). For over 30 years, EMC has been a leading provider of high performance Medium Voltage and Low Voltage Motor and Drive Systems. Services offered include: a wide variety of VFDs, custom VFD panels, engineering services, and drive repairs.
Landfill Energy Developer
Landfill gas-to-energy projects have been designed around the world to generate renewable energy from discarded and harmful waste. Landfill gas-to-energy projects are not only a significant source of renewable energy, but they also use readily available resources present in local communities to offset the use of non-renewable resources.