How to Stop VFDs From Ruining Your Motors
Common Causes and Solutions for VFD-related Electric Motor Failure
Electric motor breakdowns are the source for plenty of business for service companies, but even they would never wish it on a customer. Motor experts would rather save you the expense and downtime with well-maintained motors that run for years to come.
Maintaining motor quality takes more than regular cleaning; it depends on units working well with your variable frequency drives (VFDs).
These drives are a necessary part of many applications, but they also can be their ruin. In the worst of cases, we’ve seen drive issues take 24 motors out of operation in just six months. At best, unsolved drive issues will take several years off the life of your motor.
These problems are avoidable if you work with knowledgeable technicians who know what’s best for your system and budget.
VFDs: They’re Necessary But Come With Drawbacks
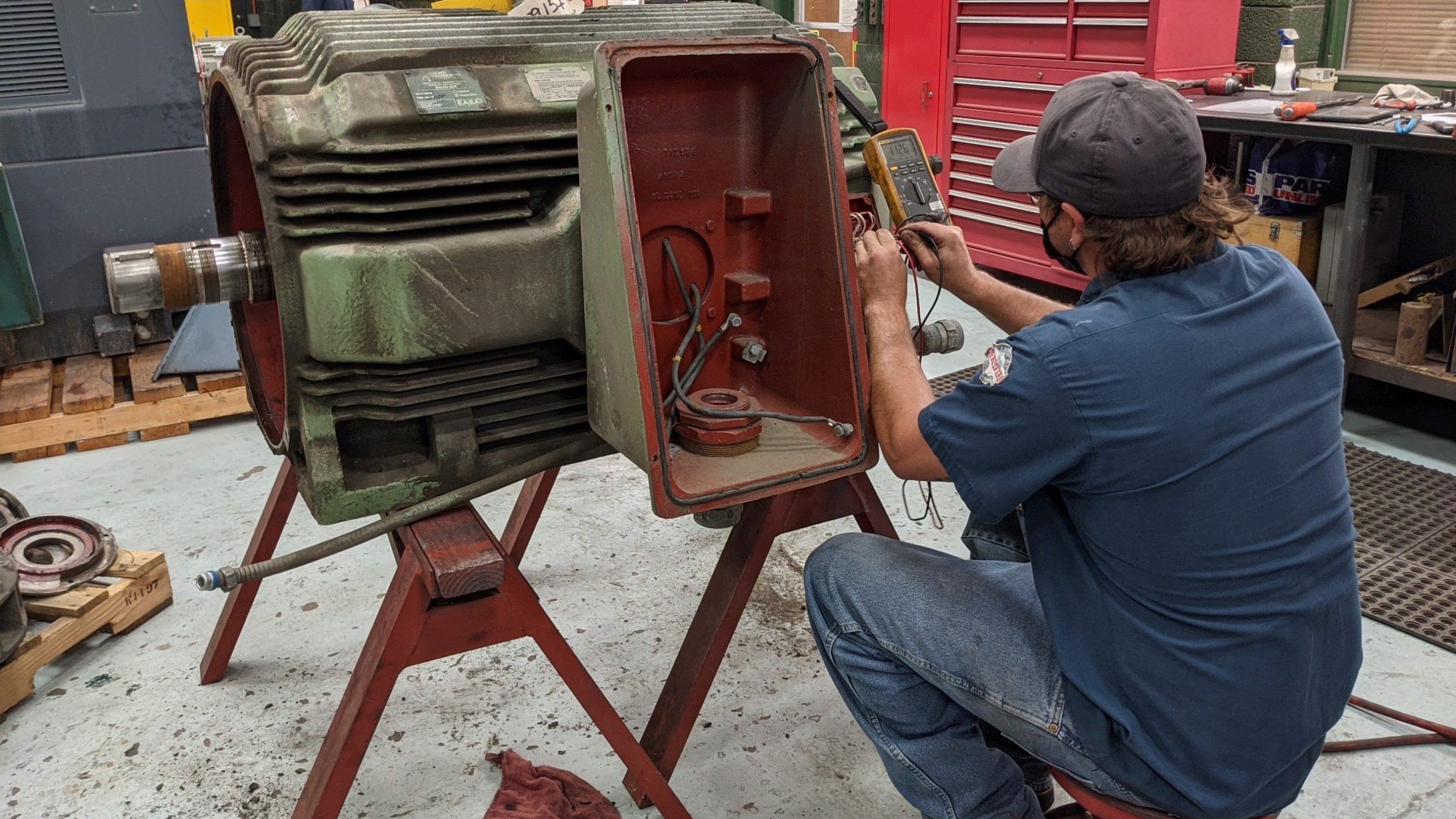
VFDs are used to start and control the operating speed of electric motors. They also save money and conserve energy.
However, improperly configured drives cause immediate and long-term problems that include very large motor repair bills. In some cases, motor manufacturers void warranties due to VFD-related failures. For example, some types of bearing failures are attributed to VFD operation, and motor manufactures won’t cover the repair costs in the event of a failure.
In addition, VFDs create harmonics that pollute the power supply. Unless you want the utility company at your door, you’re going to need a plan to solve these issues.
Utility companies manage harmonics through a standard known as IEEE-519. To help meet these requirements, qualified systems integrators can add harmonic mitigation systems like passive harmonic filters, higher-pulse VFDs and active harmonic filters.
Even if you have a well-written specification that manages VFD created harmonics, you may not have the proper protections in place for the load-side issues VFDs can create. Load-side issues tend to be more difficult to cover with “catch-all” solutions like filters.
Here are five data-backed ways VFDs damage motors as well as some likely solutions. This information will be useful if you want to make sure you are getting the best equipment for your needs.
(1) VFDs Damage Motor Windings
Damaged motor windings are the most expensive issues VFDs often cause. Copper isn’t cheap and neither is craftsman labor, so a rewinding job can cost you more than half the sticker price of a new motor. And it’s generally going to take more than a couple weeks to do. Unless you’ve got replacement motors, get ready for lengthy downtimes.
This problem is caused by extreme peak voltages. VFDs control motors with a simulated AC sine wave known as pulse width modulation (PWM). This process creates peak voltages high enough to break through motor insulation and short out windings.
That’s why any motor run by a drive should be VFD-rated, AKA inverter duty.
VFD-rated motors with premium VFD insulation (specified as NEMA MG1, Part 31) can withstand frequency peaks. But there’s a lot of misinformation out there about what constitutes a VFD-rated motor, so look for “premium VFD insulation” as set in NEMA MG1 Part 31 when purchasing new motors.
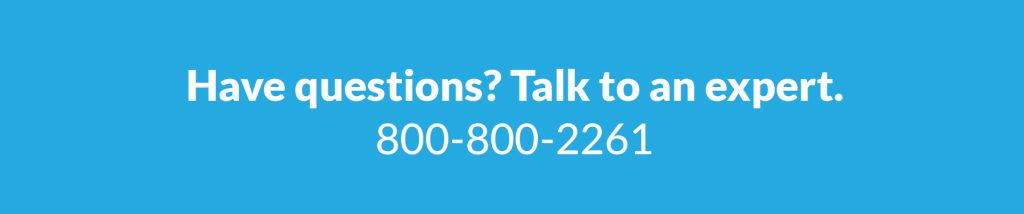
(2) VFDs Destroy Motor Bearings
Motor bearing failure is the most frequent issue caused by VFDs. While one bearing repair job could cost roughly a third of a rewinding job, the operation will pay more in the long run if the root cause isn’t addressed. Then you can tack on a week or more of downtime for reconditioning, unless you’ve got a replacement motor handy.
Unmitigated shaft currents can turn polished motor bearings into inoperable hunks of metal. Even VFD-rated motors are vulnerable.
VFDs cause electric currents to run through the motor and discharge into unprotected motor bearings. This process causes pitting, frosting and fluting in bearings and races. Equipment doesn’t last long under these conditions.
You can redirect and neutralize the effects of shaft currents a few different ways. Solutions like shaft grounding rings, grounding straps, ceramic bearings, insulated motor housings and even coated bearing races are all viable options, pending on your specific situation. Work with one of our sales engineers to determine what solutions are best for you.
(3) VFDs Burn Up Motors
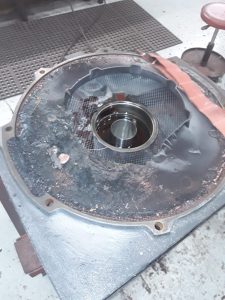
If you’ve got a burnout of this nature, you probably need a new motor.
This rests at the very root of electric motor design. VFDs are generally used to run the motor under full speed. Unfortunately, a motor’s cooling fan is attached to the rotor, so when your motor slows down, so does the cooling fan. Thus, a slow-running motor is probably a hotter motor, and hot motors don’t live very long. That’s why using a VFD voids the service factor in a traditional sense.
A larger factor offers an extra thermal margin that lets the motor stay cool. A motor with a service factor of 1.15 or more on the nameplate should be able to handle the heat unless you’re continually running at very slow speeds.
If you regularly run slow and need additional cooling, a constant speed blower can help, no matter the operating speed.
(4) VFDs With Long Leads Increase Peak Voltages
Long motor lead applications cause the drive’s PWM pulses to build on each other, like voices in a chorus, creating peak voltages strong enough to quickly break down motor insulation and short windings.
It can happen to the highest quality VFD-rated motors. We’ve seen eight 500 HP Baldor motors burn out with less than 400 feet of lead in under three months. And if 1500 volts can burn up a Baldor, they’ll burn up anything.
Take a hard look at applications with cable runs longer than 100 feet. There’s probably a reason you need such a long lead. That also probably means you don’t want to move your motors very often, like when you’ve got them at the bottom of a deep well. So make sure everything is perfect the first time, and don’t risk the cost and downtime of something like pulling submersible pump motors.
The simplest solution is to get a “soft PWM” drive that automatically adjusts its transistor switches to limit voltage spikes on NEMA MG1 part 31 motors.
You also can install a dV/dt filter on the VFD output. That usually limits peak voltage spikes to about 975 volts on a 480-volt system. If your motor meets the NEMA MG1 part 30 or 31 standards, a dV/dt filter works well for most situations.
Then there’s the premium option — add sine wave filters on the output of the VFD. A sine wave filter converts the PWM wave into a clean sine wave that doesn’t let voltage peaks exceed ~800 volts on 480-volt systems.
Sine wave filters work extraordinarily well but often cost as much or more than a VFD chassis. If your operation can’t afford a breakdown, the investment will be worth it.
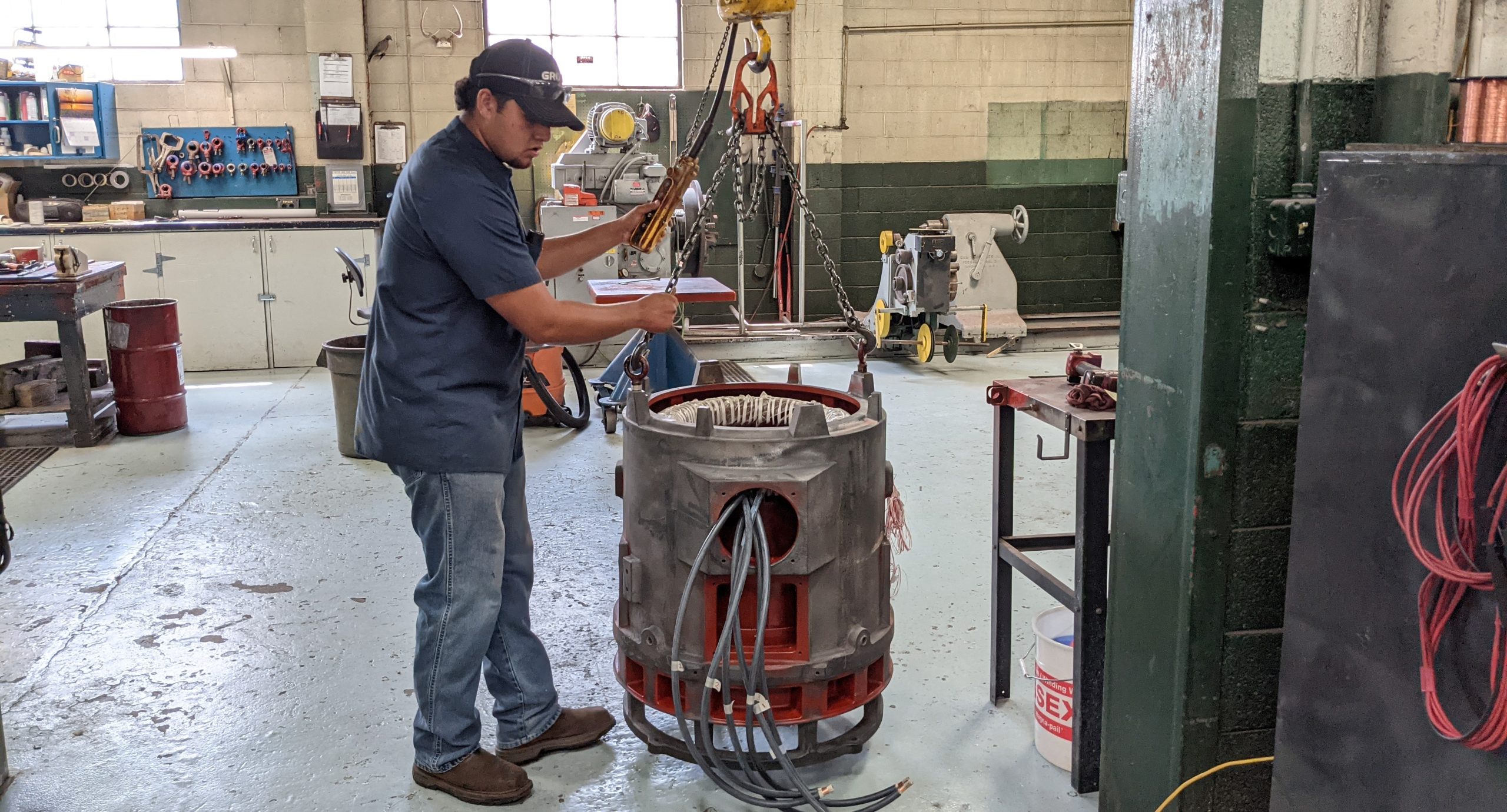
(5) VFDs Accelerate Mechanical Breakdowns
Are you overspeeding any of your motors with a VFD?
Generally, this is done to compensate for some sort of mechanical limitation.
Overspeeding motors with VFDs can result in a variety of motor-related mechanical issues. This problem generally begins with increased vibrations. It then cascades into accelerated bearing wear, general balancing failures, and complex system vibration issues that can cause failures on the driven equipment.
If you are overspeeding a motor with a VFD, you should increase your awareness of that motors alignment and vibration readings to prevent unnecessary failures.
Do You Know Why Your Motor Died?
The common drive-related causes of motor failure are very different. But unless it’s a catastrophic breakdown, it can be difficult to know exactly why a motor failed. Often, they just stop working and it takes some careful troubleshooting and/or sophisticated testing to figure out why.
Don’t just go tearing apart your motor to see what’s wrong. Disassembling a motor makes it impossible for an expert to perform certain tests that will be much more effective than someone just poking around in the components. If you take it apart, the motor shop will have to put it back together again to figure out what’s wrong.
Working with the right motor, VFD and accessories will eliminate most of your problems before they occur. Check out our wide selection of electrical components to find the perfect options for your system.
If you don’t know why your motor failed or need help preventing a known problem, give us a call. We’ll gladly make house calls for customers located within one of our service areas.
Our service locations include: