Medium Voltage VFD Maintenance
What is the first consideration with Medium Voltage VFD Maintenance?
Almost every company spends a lot of money and time setting up their safety programs, processes, and safeguards. However, these same companies will not hesitate to send an under-trained internal technician to work on equipment which could result in serious injury. From my experience, this doesn’t come from an intentional effort to be unsafe, but simply a lack of understanding the potential job hazards.
Although dangers change from site to site and application to application, there are many things to consider when attempting to perform electrical maintenance. Medium voltage (MV) equipment poses enhanced risks with those who are unfamiliar with how they work because this equipment tends to be less understood. However, even a low voltage arc flash event, can produce a more powerful event than a lightning strike, meaning that working with switchgear, VFDs, or any live equipment can be extremely dangerous if the worker is not properly trained and protected with appropriate PPE for the task. Properly Locked out / Tagged out equipment that has been proven to be de-energized, will help to ensure a safe working environment for equipment and your employees.
At no time should an un-qualified person attempt maintenance or access Medium Voltage equipment.
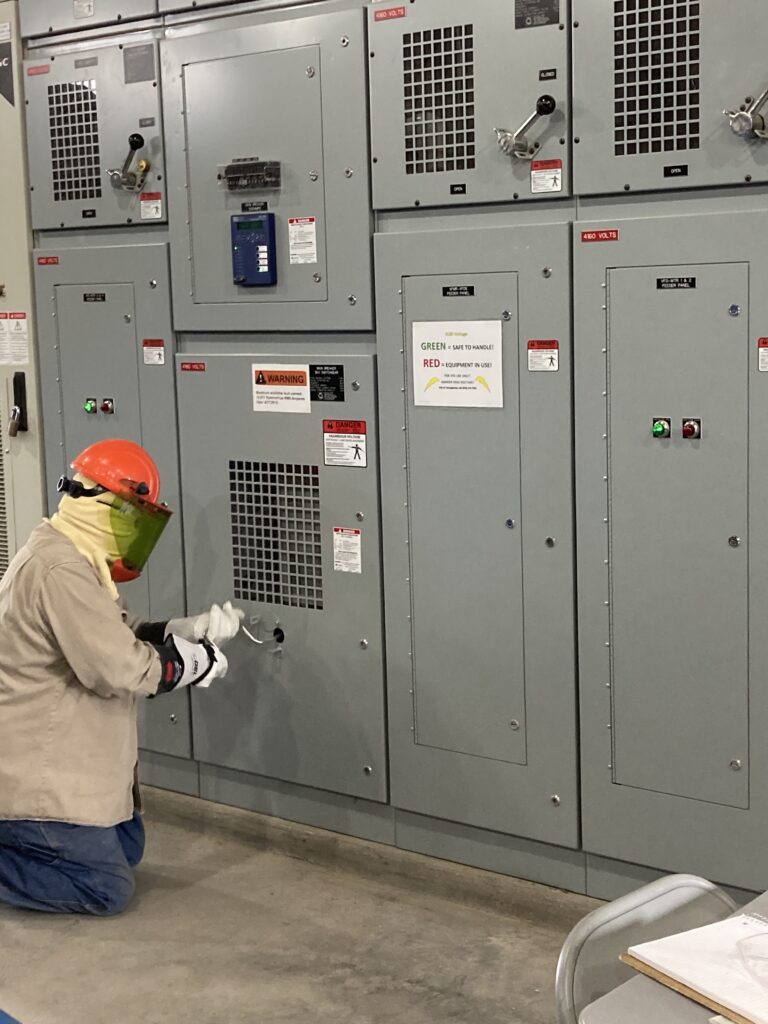
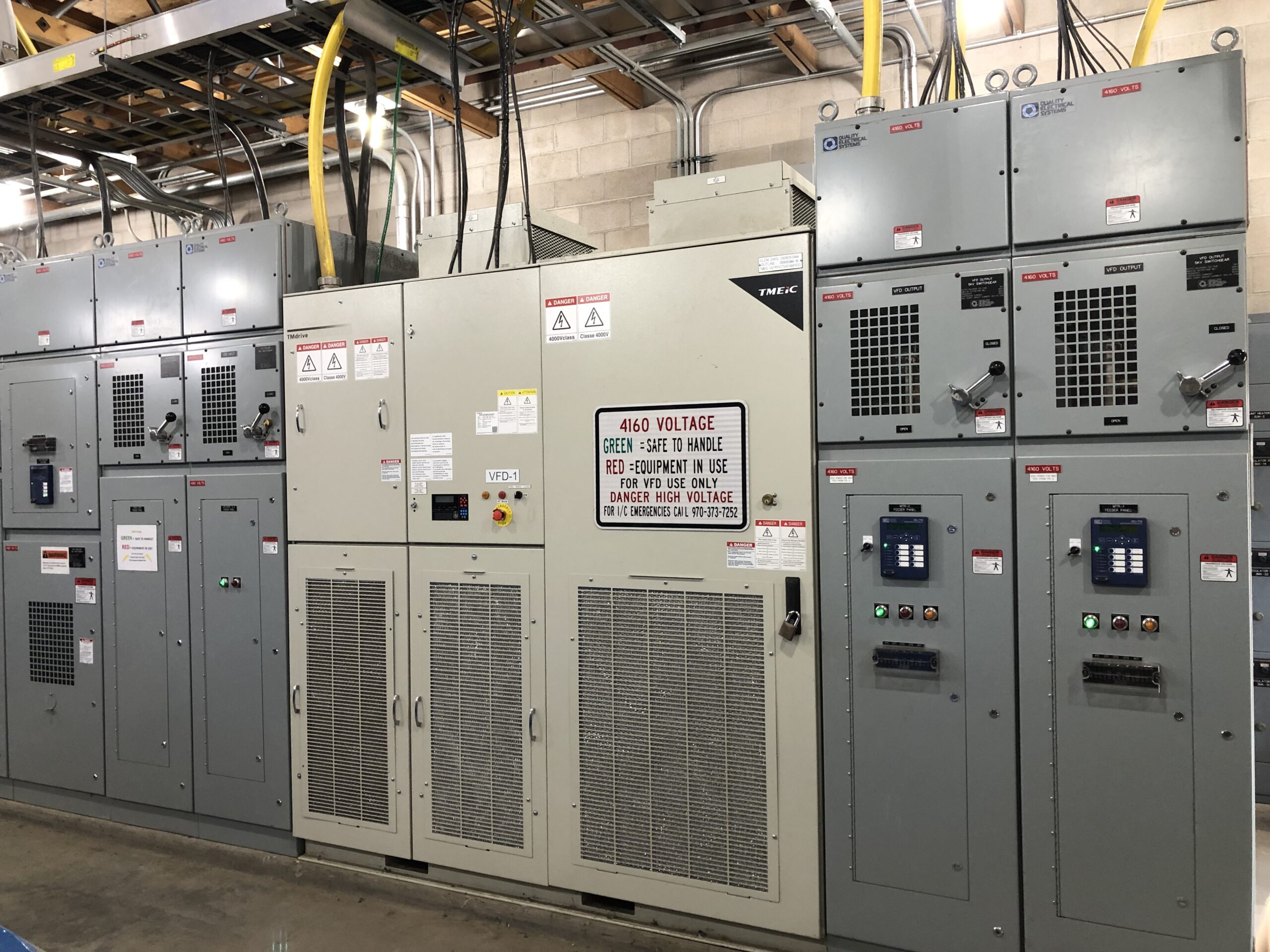
What are the recommended service maintenance intervals for MV VFDs?
MV VFD maintenance programs should be developed and implemented considering some key items.
- Criticality of operation
- Downtime expense (do to failure)
- Cleanliness of environment
- VFD Properly sized and designed for the application
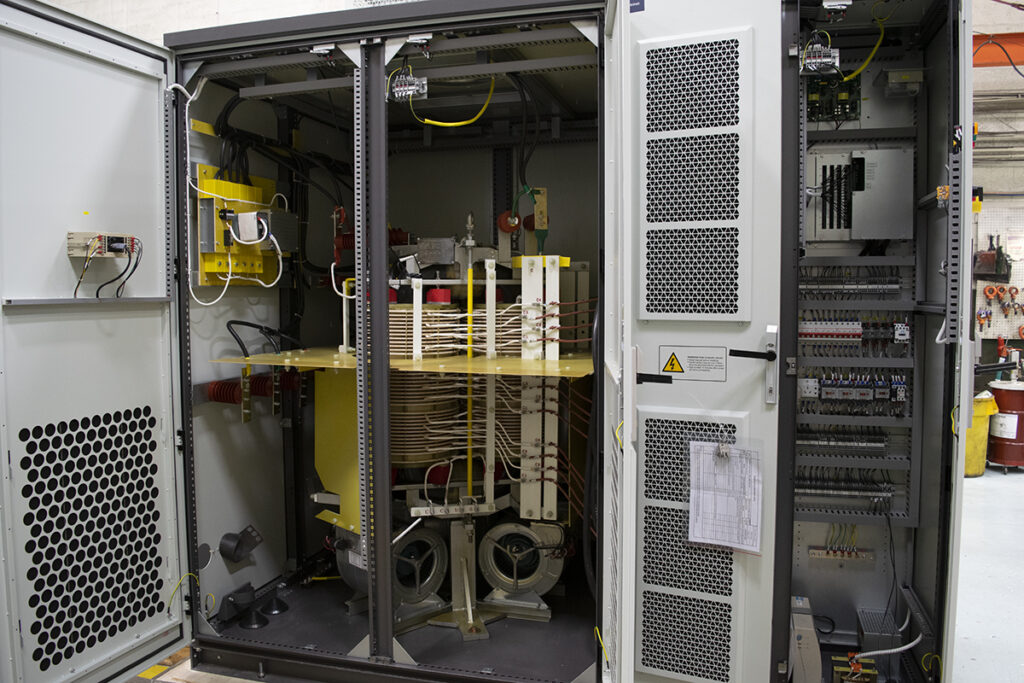
Typically, it is suggested to perform at least two levels of maintenance:
(1) Weekly, monthly or quarterly inspections depending on environment and operating conditions. It can be performed by operator or electrician as there is no need to access the drive internals or live components.
- Perform cleaning and inspection of all filter media in air cooled ventilation system
- Cleanliness of environment for long term operations
- Visual and audible inspections for any signs of problems
(2) Yearly full system inspection, cleaning and verification of operation. Typically performed by trained and competent / qualified personnel only.
- Perform complete inspection of all power connections, wiring and connectors for signs of heat damage or loose connections
- Verify all control and power connections of proper tightness
- Cleaning of all power components to ensure proper ventilation or cooling
- Verify all power fuses for proper connections and continuity
- Verify fan operation is free and un obstructed with no visual or audible problems
- Perform complete inspection of all control connections and Printed Circuit Boards (PCB’s) to identify any abnormal discoloration or loose connections
- Verify proper connections of all fiber optic cables and connectors
- Verify all heat sinks are free of dirt, debris, or foreign matter
- Verification of programming, parameter settings and complete operations
- At a minimum, perform megger testing of motor and cables to ensure integrity of insulation to ground
Don't Go At It Alone! Call Us.
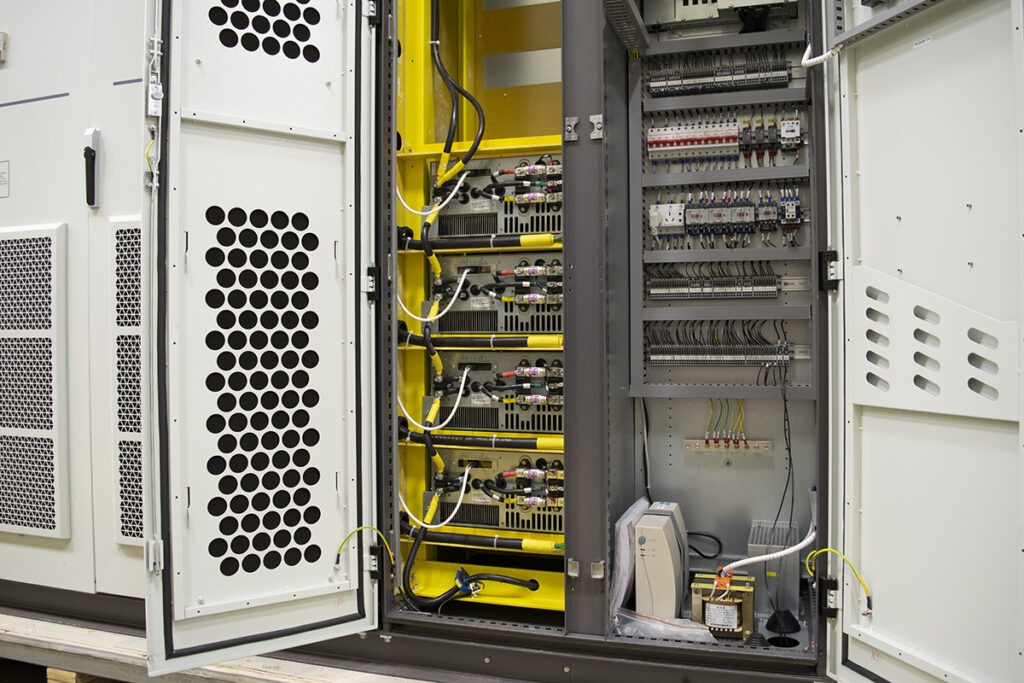
When will equipment warranty require a factory-trained and authorized technician?
Many products require a factory-authorized technician to commission the equipment in order to validate a warranty, or extend the normal duration. It’s not uncommon to see manufacturer’s double or triple their warranty when they know it was started up by a technician they have trained and trust. Many warranties even require preventative maintenance by these same technicians at regular intervals. The cost of a technician can often pay off in the long term because it prevents future problems from becoming expensive headaches by keeping them under warranty.